Medical injection molding
Injection molding is a manufacturing process we use to produce plastic devices in either large and small volumes, which is used also in the medical field for the production of a wide range of medical plastic devices. What differentiates common injection molding from medical injection molding is the fact that the latter must be absolutely compliant to the strict FDA regulations for what regards Food, Drug and Cosmetic products.
On this page we will deepen:
Molds for the medical sector's specifics
In the medical sector, molds used for producing plastic parts must meet stringent requirements. Dealing with plastic materials used in medical devices assumes continually developing innovative products, focused on the security for the doctor and the patient; as such we work in PC, PEEK and Ultem plastic materials to develop medical applications for multiple uses.
The most critical specifications of molds for the medical sector are:
- Precision is of utmost importance, as the plastic parts used in medical devices must be designed and produced to exact specifications. Even a small error can have serious consequences, so the molds must be able to deliver extremely precise results, often to within a millimeter or less.
- Molds use for medical applications must also be designed with hygiene and ease of cleaning in mind. Medical devices must be sterile and free from any contaminants that could compromise patient safety, so the molds used to produce them must be easy to clean and sanitize thoroughly.
- Another key characteristic is their suitability for both high-volume and small-scale productions. Medical devices are used in a variety of settings, from hospitals to home care, so molds must be able to produce products in large quantities for mass distribution, while also allowing for smaller, more customized runs.
- Resistance to different manufacturing environments is also important, as this type of molds must be able to withstand the rigors of various production methods, including injection molding and thermoforming.
- Toughness is a must, as molds must be able to withstand the wear and tear of continuous use in the manufacturing process.
Molds for the medical sector must be able to deliver precise, hygienic, and reliable results, with the flexibility to accommodate both large and small production runs, and the durability to withstand the challenges of different manufacturing environments. With the right molds in place, manufacturers can develop innovative medical products that prioritize the safety and security of doctors and patients alike.
What is medical plastic injection molding used for?
Medical device plastics are characterized by great versatility and can be combined even with metals. So, they are employed in a various range of medical parts, components and products such as:
- Needles
- Surgical instruments and blades
- Medical enclosures and knobs
- Tubes
- Dental instruments
- Medical equipment components
- Prosthetics
Read more here: What is medical plastic molding and how does it work?
What we offer as medical injection molding suppliers
Since 1986 we have been working as medical injection molding suppliers and manufacturers (and also for many other sectors), by offering a service that includes:
- Co-designing – If you need molds with an uncommon shape, we are able to provide it thanks to our service of custom mold design
- Designing and engineering – We put the most maniacal attention to details by combining our expertise with a state-of-the-art technology (CAD/CAM/CAE) to meet all the specifications you need
- Prototyping and pilot molds – Medical injection molding and medical insert molding are the most used techniques for mold prototyping: the choice depends on the kinds of plastics used
- Mold construction and tests – We conduct in-house final testing of the medical molds
The benefits of medical plastic molding
While requiring the highest precision – which we are able to achieve through our precision injection molding service –, injection molding for medical parts provides also benefits like:
- cost-efficiency
- production of durable medical parts, components and products
- suitability for high and small volume productions
- production of plastic tools and applications that requires consistency and tight tolerances
Read more: Plastic injection molding for medical parts
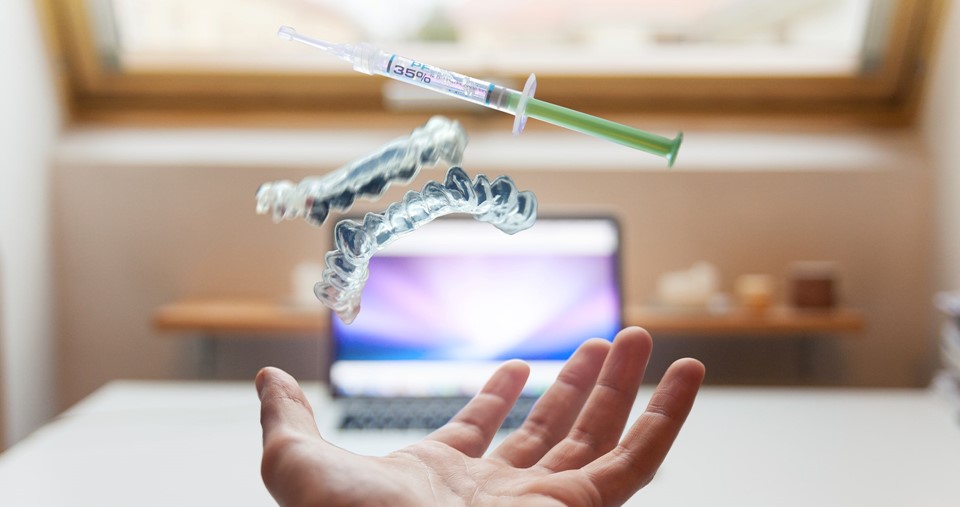
Understanding medical device injection molding
Medical device injection molding is a specific and highly specialized field which requires accuracy and the perfect adherence to the rigorous FDA standards.
When it comes to medical device injection molding , there are multiple stages which need to be followed.
- Prototyping: in this phase, we usually design the mold thanks to computer-aided software which helps us to visualize the 3D model. It is of the utmost importance to assess materials, the shape of the tool itself and its use in the medical field. In the medical field, these molds should not only be extremely accurate, but functional as well.
- Testing: at this point, the medical mold prototype needs to undergo a test stage. In this case, it is crucial to observe the mold and how it responds to real-life situations. In this way, it is possible to change the design of the mold in order to align it to the production and market requests.
- Process validation: the injection molding should be approved so that it is compliant with the specifications and quality standards set by the FDA for the medical sector.
- Quality measures: quality control should be implemented throughout the entire manufacturing process in order to verify that every medical device is impeccable. As a matter of fact, quality control for us means monitoring; quality checks on our medical devices so that we can immediately detect failures or defects that could potentially have serious consequences on machine operation systems and technologies as well as on people’s health; and reports about the overall results.
Choose our medical device injection molding
Contact us free of charge
Quality control and traceability
As medical injection molding suppliers we put much attention to quality standards and parts traceability throughout all our manufacturing steps.
As a matter of fact, tracking back devices and processes is fundamental in the medical industry as a single failure or defect can have serious consequences on machine operation systems and technologies and, of course, on people's health.
Choose our medical injection molding service
Contact us free of chargeAll the plastics we use in medical injection molding
Materials are crucial in medical plastic molding as the resulting products must comply with the European FDA laws. At Idea Stampi we use medical grade plastics with high molecular weight and chemical and heat resistant properties.
The most suitable materials for injection molding in the medical industry turns out to be:
- Polycarbonate PC – Due to its high tensile, flexural and shear strength, heat resistance and low moisture absorption, this material is most used for the supply of medical tubing
- Polyether ether ketone PEEK – Suitable for food contact, it is a plastic resin highly resistant to chemicals, fatigue and cracking: medical devices made from PEEK can be easily sterilized by autoclave
- Ultem – A kind of plastic which is ideal for medical tools as it is resistant to environmental stress and high temperatures, while offering excellent dimensional stability: also the products made from Ultem can be sterilized by autoclave
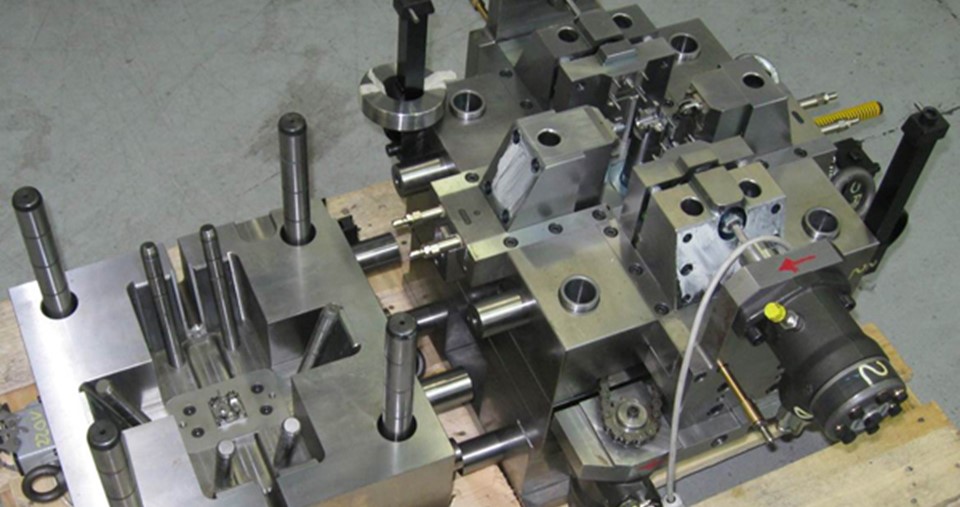
Selecting injection molding medical plastics
The above listed materials are just a few compared to the various kinds of plastics used in injection molding for the production of medical parts and products.
However, despite the great variety available, all plastics used in medical injection molding share some features, which are:
- Strength – As plastic resins have different level of strength, it is important to select those which have the properties required by the final application
- Resistance – Chemical and heat resistance are critical factors as the medical products born from injection molding must usually undergo sterilization by autoclave, gamma ray or various chemical methods
- Resistance to operating environment – Materials are to be chosen with the operating conditions in mind as they determine strength, temperature, resistance to heat, chemicals and corrosion of the final products
- FDA Requirements – Last, but not least, medical plastics must meet the strictest FDA requirements: for instance, medical devices to be implanted have different specifications than tubing and other medical instruments, which are explained in the FDA regulations
Choose Idea Stampi as your medical injection molding supplier
Contact us without commitment