Laser welding for mold repair
In 2009, we added another service to our offer: injection mold laser welding. It is an innovative system that allows modifications and refurbishing on already-existing molds without overheating the part or creating damage, distortions or tempering which cause loss of characteristics.
Laser welding is typically used to:
- Build up damaged or worn up surfaces
- Fill in small voids
- fix cracks or mistakes
- Accommodate engineering changes
- Repair parting lines
The welding process allows us to assemble many materials such as steel, bronze, copper, aluminum and titanium alloys, with a hardness of up to 60HRC in order to meet all customers’ demands.
Understanding laser welding
Laser welding is a working method which employs laser beam to melt materials to execute maintenance operations or repair molds. Unlike traditional welding, the laser technology allows carrying out flawless repairing procedures without compromising with high temperatures the surfaces surrounding the mold.
Furthermore, thanks to advanced and accurate machines, it is possible to reach even the smallest areas, enhancing the overall efficiency of the process as pre-welding preparations are not necessary anymore. In this way, the workflow is swifter, reducing the operator’s strain and extending the molds’ lifespan.
How to use laser welding to repair molds
Surface defects and structural damages can undermine the performance of your mold. This is when laser welding is needed, as this advanced technique can easily address any problems your mold may present, restoring its original effectiveness.
With a laser beam, the damaged areas are welded. The mold structure is accurately modified in order to preserve its integrity and reducing potential distortions. During the process, the dimensional precision of the mold is maintained, ensuring consistency in the production of components and without replacing the damaged mold.
Nowadays, laser welding is an invaluable resource because, in comparison with other repair techniques (grinding or machining), it is way superior as for the quality of the final result and turnaround time, guaranteeing an efficient production cycle.
Do you need mold repair?
Choose Idea Stampi laser welding technologyCarrying out laser welding for molds
The most common way to repair a mold is laser welding. As a matter of fact, this process can restore the mold to its original and optimal condition by eliminating or sensibly reducing the problems that can arise, instead, with traditional welding. That is, laser welding can increase mold life while improving the whole manufacturing process.
Laser welding for mold repair is usually carried out through four gradual steps:
1. Damage analysis to determine the damage degree
2. Defects inspections to find the source of the damage
3. Removal of the damaged material to restore the mold to a like-new condition
4. Injection mold laser welding - A filler rod is usually placed between the worn or the damaged surface and the laser beam. The latter fuses the filler rod with the base material and repairs the area (a microscope must be used to target the weld point, while a filler rod fills in voids).
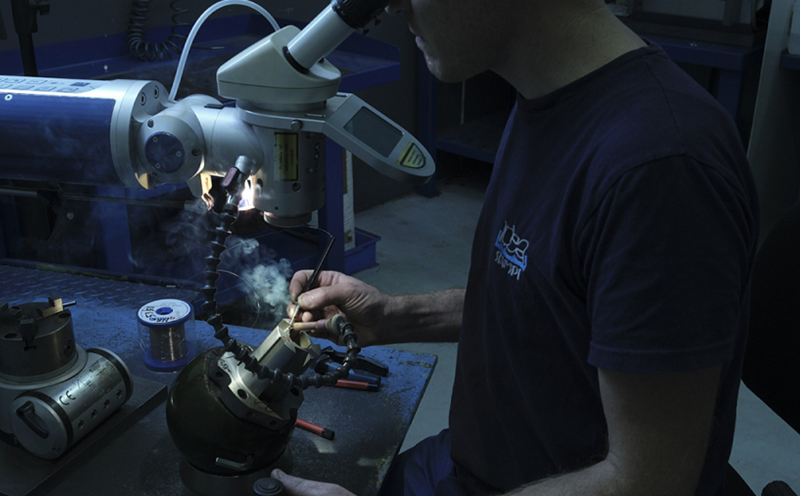
The benefits of injection mold laser welding
There are several reasons why we have chosen laser welding for injection mold repair. One of the most important ones lies in the fact that laser mold welding is way cheaper and faster than making a brand-new mold.
Other reasons regard the advantages of laser welding for mold repair over conventional TIG and micro-TIG welding:
- It offers higher return on investment as it reduces rework and finishing costs
- It offers a high degree of heat localization and controllability, which makes it the ideal choice for repairing complex molds too such as the custom-made ones used in the design field
- It makes the entire mold remain cool to the touch, preserving its original shape
- The sink of the base material that surrounds the welded area is remarkably reduced as the quantity of metal drawn into the melt pool is minimum
- Laser welding for molds also reduces the amount of finishing, machining and handwork required
- It can be used to repair a great variety of materials, including non-ferrous ones such as copper and aluminum, which do not stand micro-TIG well.
Why laser welding for molds repair is superior to tig and plasma welding
Let us now see how laser welding for mold repair is superior to TIG welding and plasma welding. First, the laser generates a much lower heat input than TIG and plasma welding. This means that:
- By generating a smaller thermally altered zone (HAZ), laser welding for injection mold repair is exceptionally more precise;
- Provides greater control over the area to be welded;
- Allows a greater variety of material combinations
- Ensures the absence of pitting and internal defects;
- Does not require pre- and post-weld treatment;
- Is faster.
Laser welding mold repair also makes it possible to reach parts that are hidden or surrounded by delicate elements, making mold repair impossible if another method is used.
Our service of laser welding for mold repair
Our laser welding mold repair process includes a few steps, which are necessary to carry out a defect-free repair:
#1. Analysis of the part to be repaired - At this stage, the engineering department investigates the damage to be repaired in the mold, which may be a crack or a worn spot.
#2. Visual inspection. Once the defective part is identified, we perform a visual inspection with magnification and, if necessary, penetrating dyes (PPE) or fluorescent dyes (FPI).
#3. Removal and repair. In this final stage, we remove the damaged material and then work on the reconstruction of refurbished steel to restore it to its original condition.
Eventually, our mold maintenance service ranges from standard cleaning to more complicated interventions such as the reconstruction of worn parts. We are able to perform maintenance interventions within 24/48 hours so that you don’t have to deal with long downtimes.
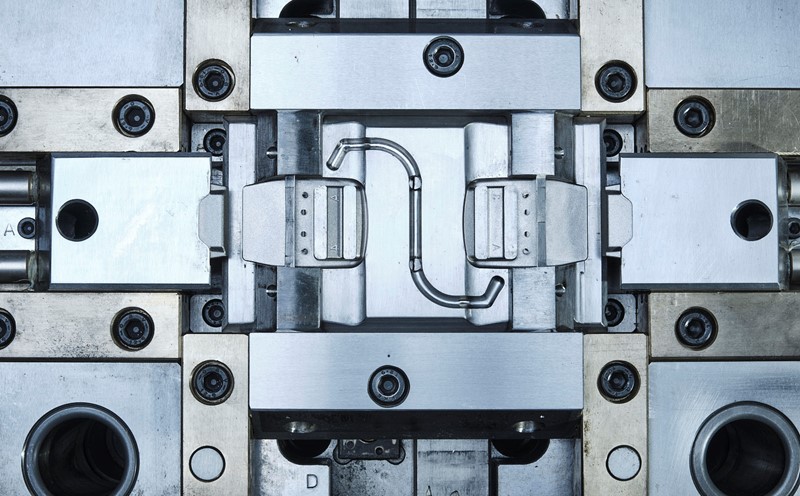
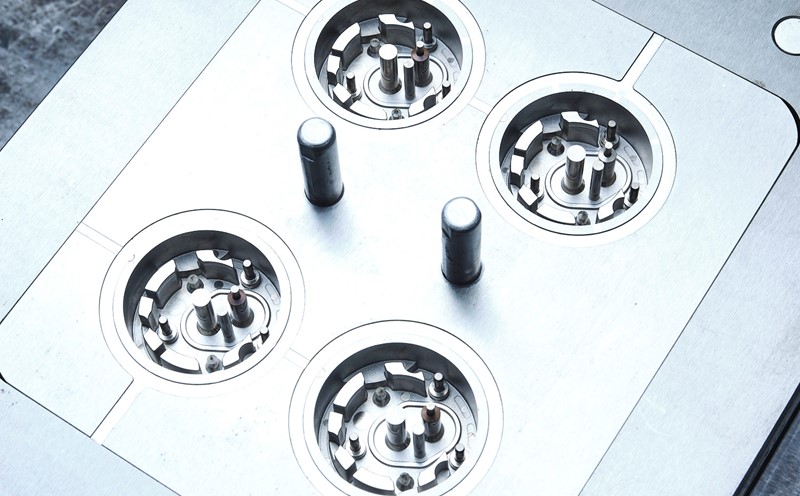
Do you need mold repair?
Contact us for more information