Plastic gear molding: advantages and considerations
Plastic gear molding has emerged as a manufacturing technique for producing high-quality, durable gears with complex shapes and precise tolerances. Unlike traditional metal gears, plastic gears are lightweight, resistant to corrosion, and offer excellent noise-reducing properties. In addition, plastic gear molding is a cost-effective process that offers faster cycle times, greater design flexibility, and lower tooling costs than alternative methods. However, before deciding to use plastic gear molding, it is important to consider various factors such as material selection, design considerations, and manufacturing process requirements. On this page, we will explore the advantages and considerations of plastic gear molding, and provide insights into how it can be used to produce efficient, high-performance gears for various applications.

Advantages of using injection molded plastic gears
Injection molding to produce gears and other plastic components has many advantages. Below are some main ones:
- High-precision.
- Injection molding allows good replication to maintain manufacturing standards.
- It is low-cost processing: most plastics get processed at temperatures well below those needed for stainless steel. This reduces the energy and time consumed in heating and cooling.
- Plastics do better at resisting abrasion and wear than metals. This is even more so in high-performance plastics. This results in more durable parts.
- Plastics do not rust, unlike metals.
- Plastics offer more design options. Complex designs are easier to achieve with plastics.
Contact our team to learn more about our plastic gear molding capabilities
Contact us
What to consider when injection molding gears
There are some crucial points to consider when approaching injection molding gears.
Mold construction
In order to ensure high precision in mold fabrication, the mold maker must use specialized tools for precise measurement of parts. Similarly, the tools utilized for machining and fabrication of the mold must also be of high precision. Idea Stampi specializes in the construction of molds for medium-small plastic pieces with complex reduced-size shapes, which call for utmost accuracy and precision.
Cavities
Another factor to consider is the number of cavities. Limiting the cavities to a small number helps minimize variation. This approach also shortens the distance between the injection and molding sections, which reduces the risk of uneven filling or cooling by decreasing the distance of the runners.
Uniform cooling
If there are variations in process parameters, such as time, injection speed, pressure, and shot size, they can affect the final product. For instance, the time it takes for the product to move across the conveyor belt after release impacts its cooling rate and therefore shrinkage, potentially influencing precision. To ensure uniform cooling within each mold and across all molds, there are various methods, such as precise control of flow through cooling lines and automated removal and transfer.
How do you ensure part uniformity?
The uniformity and roundness of a molded gear are influenced by the part's geometry and the number and placement of gates used to fill it. A gear with three evenly spaced gates on its face will result in an out-of-round condition with three peaks and valleys, whereas using five gates will still cause some out-of-roundness, but its magnitude will be lower since the gear diameter will be divided into five segments. This principle applies to adding more gates as well.
A diaphragm gate is highly beneficial for gears, but its use depends on the gear bore design. This gate evenly blocks the melt flow and produces a gear with consistent roundness and minimal peaks and valleys.
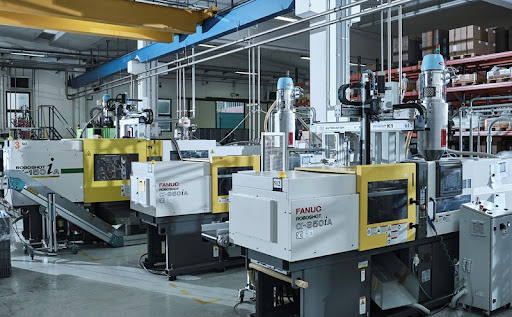
Applications of injection molded plastic gears
Injection molded plastic gears have a wide range of applications across various industries due to their numerous advantages. They are lightweight, cost-effective, and have excellent strength and durability. Additionally, plastic gears can be molded into intricate shapes and sizes that are difficult to achieve with metal gears. These qualities make them ideal for use in:
- small consumer electronics;
- toys;
- automotive parts;
- medical equipment;
- food industry.
With advancements in technology, injection molded plastic gears continue to be improved to provide high precision, low noise, and better heat resistance. Overall, the versatility and performance of injection molded plastic gears make them an attractive option for many industries.
The difference between injection molding plastic gears and machined plastic gears
Injection molded gears and machined gears are two different manufacturing processes for producing gears.
The injection molding process involves injecting molten plastic material into a mold, which cools and solidifies into the shape of the gear. In contrast, machined gears are created by cutting or shaping the gear material using machine tools. This process is generally more costly and time-consuming than injection molding.
The main differences between the two processes are:
- Cost – injection molding is cost-effective;
- Manufacturing time – faster in injection molding;
- Quantity and quality – injection molding allow a larger production volume.
Specialized quality assurance for plastic gear molding
Founded in 1986, Idea Stampi started as a mold construction enterprise and has since specialized in polymer injection molding, including injection molded gears. Recently, we have taken a significant step forward by acquiring press machines that enable us to achieve two critical objectives. Firstly, we can now manage the entire production process in-house. Secondly, we can provide a comprehensive thermoplastic injection molding service from start to finish, covering pre-production batches and delivery of the final products.
Contact our team to learn more about our plastic gear molding capabilities
Contact us