PEEK injection molding
PEEK (polyether ether ketone) is a versatile and useful resin for injection molding processes. Idea Stampi is specialized in both injection molding for PEEK and manufacturing custom molds for PEEK. This material is ideal for medical applications because of its tolerance to gamma-ray exposure and sterilization processes and is also used to replace metal parts in a wide range of industries (i.g. aerospace, mechanical, and other demanding applications).
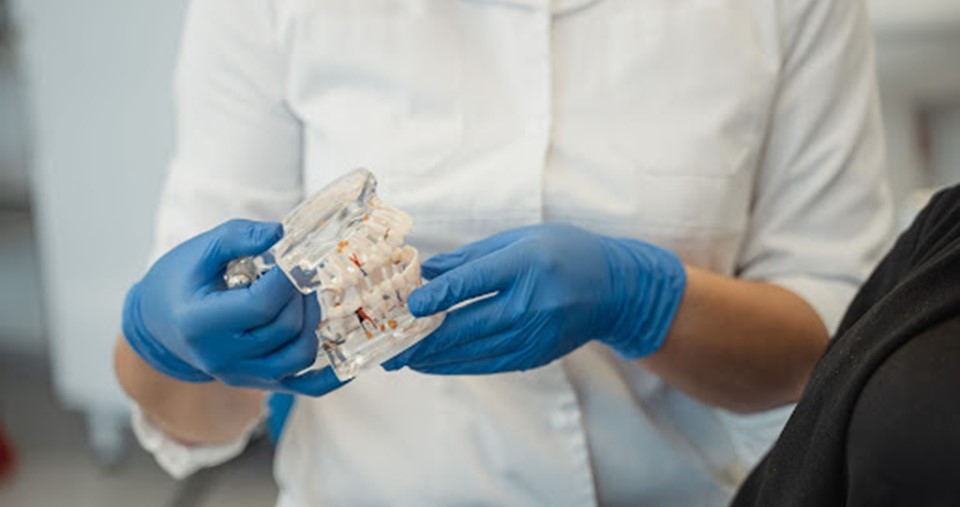
How PEEK Injection Molding Works?
PEEK is the acronym which stands for Polyether Ether Ketone. This is a semi-crystalline thermoplastic resin that is commonly used for injection molding for its accuracy and resistance to high temperatures.
PEEK injection molding is performed by taking the material at its melting point in order to obtain a fluidic state that allows to insert it into the mold cavity. This technique is quite complex, yet it ensures excellent results in terms of dimensional precision and tolerances. In this way, it is possible to manufacture components that guarantee perfect durability.
What Are PEEK Main Properties And Operational Advantages?
PEEK is a material that features multiple core characteristics, which make it an excellent choice for a wide range of industrial applications.
Among its properties is important to highlight:
- Mechanical strength: PEEK is particularly suitable for heavy-duty sectors, demonstrating its structural integrity even under stresses and strains, making it highly resilient.
- Excellent dimensional stability: the material displays minimal expansion or shrinkage, maintaining its precise dimensions.
- Flame resistance: PEEK is hardly flammable and self extinguishing, meeting stringent fire safety standards.
- Low smoke emission: it produces very low flue gas density under combustion.
- Temperature resistance: the material can endure extremes from as low as -60°C to as high as 260°C in environments such as hot water or steam.
- Low coefficient of linear expansion: in the PEEK injection molding process, where temperature variations are an integral part of the process, the material features minimal dimensional changes, guaranteeing the reliability of the whole process.
Learn more about polymer injection molding at Idea Stampi
The Several Applications of PEEK
PEEK injection molding is the perfect solution for a multitude of industries that are interested in enhancing the level of their production by using a highly performing material.
Aerospace and Automotive
When it comes to the aerospace and automotive fields, PEEK injection molding is used to manufacture components that demand high mechanical strength and excellent thermal stability. This thermoplastic resin can withstand intense pressures and temperatures, becoming the perfect choice for crafting bushings, bearings and insulation components.
Medical and Food Processing
PEEK is a biocompatible and chemical resistant. For this reason, it is often used for the creation of medical implants and sterile medical devices.
This material is also used in the food processing industry for parts that require high-temperature resistance while preserving the integrity of the product and preventing the risk of external contamination.
Oil & Gas
PEEK injection molding is a valuable technique for the production of valves, pumps, and compressors for the Oil & Gas industry. In this case, it is important to maintain their integrity even in harsh and corrosive environments.
Electronics
PEEK is renowned for its excellent insulating properties and low smoke emission. It is used to engineered and manufacture parts, such as connectors, insulators and electronic components.
Discover more about PEEK polymer mold manufacturing
The PEEK Injection Molding Process Explained
PEEK injection molding is a complex process which requires highly specialized equipment capable of handling extreme temperatures.
Let’s discover the steps of the procedure.
- First, PEEK must be dried thoroughly before using it. This is a preparation that helps remove any moisture that might lead to hydrolysis, which can compromise the quality of the final product.
- Then, the thermoplastic polymer is heated at or above 360°C (680°F). This is the temperature which causes the material to melt. Precision is key, as overheating can lead to the degradation of the resin.
- PEEK injection molding begins when the material is inserted into the mold cavity under controlled pressure. This aspect must be managed carefully to ensure a consistent and even filling.
- Once the PEEK is injected, it is now time to make it cool down. Being the resin prone to anisotropic shrinkage, it is necessary to control the cooling rate and apply the right pressure throughout the entire solidification process to maintain its structural integrity.
- Ultimately, PEEK is ejected from the mold in order to perform post-processing operations (if needed) and guarantee an impeccable quality of the component manufactured.
Are you looking for a partner for your next PEEK injection molding project?
Contact Idea Stampi!Why Should You Opt For Idea Stampi PEEK Injection Molding?
Idea Stampi is not only involved in injection molding for PEEK and other thermoplastic materials. You can also contact us for:
- The in-house production of injection molds for plastics;
- A molding service ranging from pre-production of batches to finished products.
Contact Idea Stampi to learn how we can use PEEK thermoplastic in your injection molding projects.
Contact us!